Laser welding machine is a newly developed device for easy and precise metal welding and cutting. Stainless steel, mild steel, brass and aluminum can be processed with minimum skill thanks to this technology.
Laser welding demonstration
We can arrange laser welding demonstration in your site or in our Sydney, Wetherill park workshop.
Please contact us for details
Hand-held laser welding machine adopts the latest generation of fiber laser and is equipped with a swinging hand-held welding head. It has the advantages of simple operation, beautiful welding seam, fast welding speed, etc. It can weld thin stainless steel plates, iron plates, galvanized plates and other metallic materials. It can replace most welding processes such as traditional argon arc welding and electric welding. The hand-held laser welding machine can be widely used in the welding process of kitchen cabinets, stair elevators, shelves, ovens, stainless steel door and window guardrails, power distribution boxes, stainless steel household appliances and other industries.
laser welding head
The welding head is designed with the concept of ergonomics, fully considering the applicability of the welding process and the comfort of long-term use (weight 1.0kg), and has a safety lock that touches the mouth to contact the work light for preventing accidental triggering and hurting others.

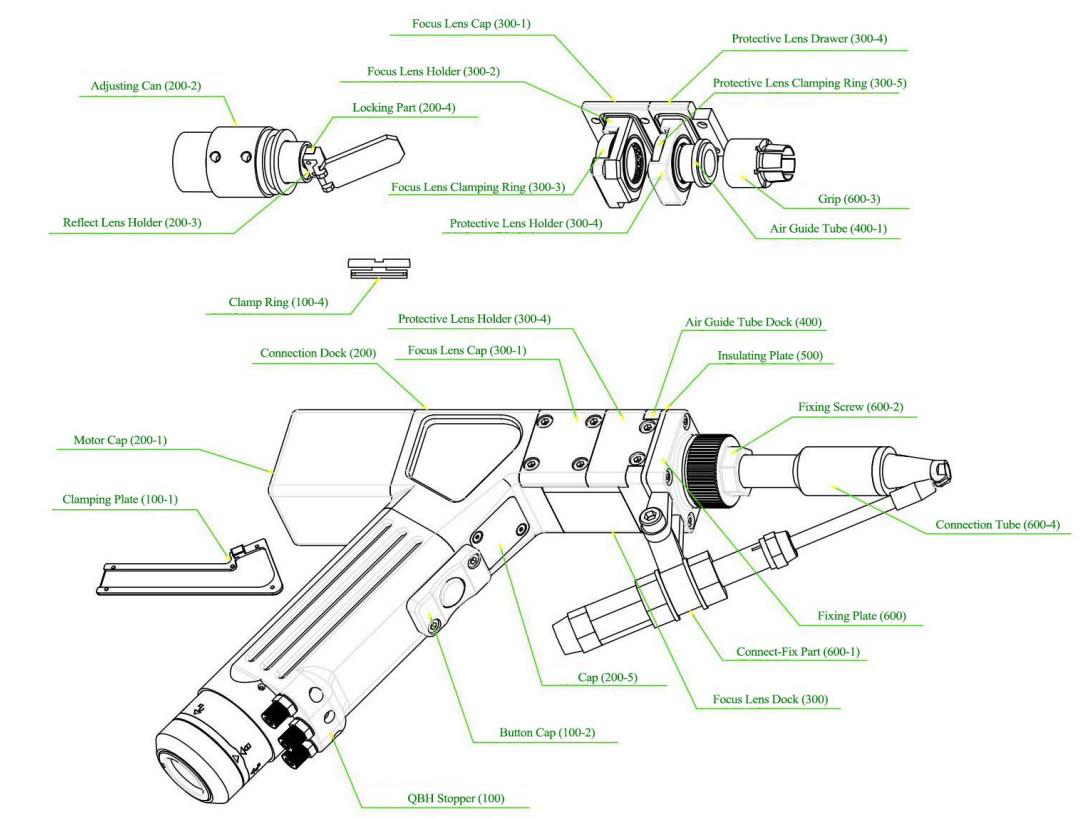
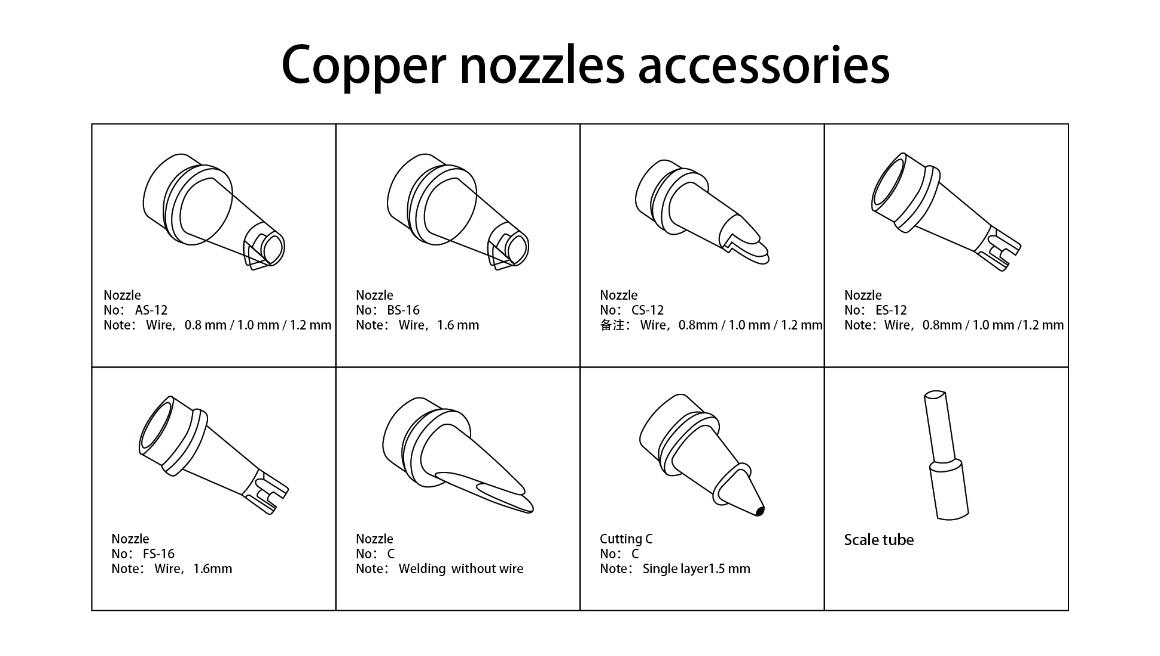
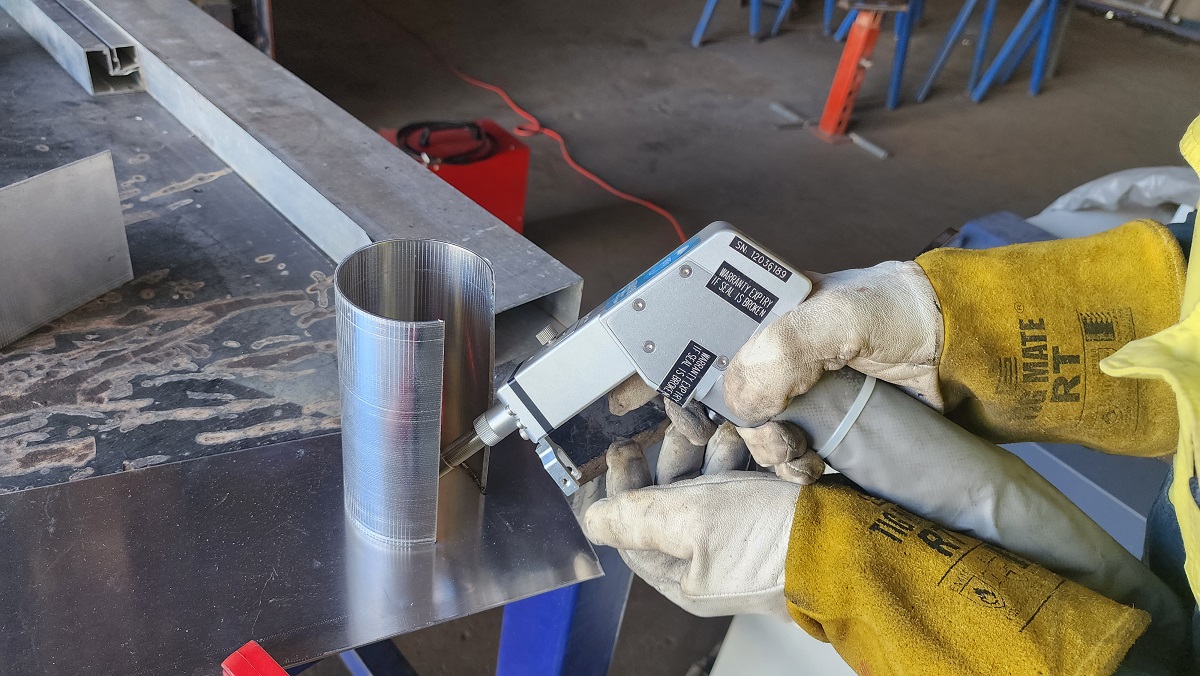
Traditional Versus Laser Welding
Compare items | Traditional welding | Fiber Laser Welding |
Workpiece heat absorption | Very high | Low |
Workpiece deformation | Large | Small |
Bonding strength to base metal | Normal | Very good |
Follow-up | Polishing | No sanding, or very little sanding |
Welding speed | Normal | More than 2 times faster than argon & arc welding |
Applicable materials | Stainless steel, carbon steel, galvanized sheet | Stainless steel, carbon steel, galvanized sheet, aluminum and other metals |
Consumables | Lots of consumables | Less consumables |
Difficulty of operation | complex | Simple |
Operator safety | Unsafe | Safe |
Environmental impact | Not environmentally friendly | Environmentally friendly |
Welding tolerance | Good | Good |
Swing welding | No | Yes |
Welding similarity | Poor | Very good |
Better welding quality
Welding constancy can be achieved by a laser welder. Welding quality and consistency improved thanks to fiber laser technology. As a result, products would look nicer and more even surfaces fabricate.
Less heat, less Distortion
Laser welder uses less and concentrated energy for melting. It mainly reduces HAZ zone and result in much less distortion in parts fabricated.
Faster welding
It speeds up welding process compared to traditional stainless steel and aluminum TIG. As a result, laser welding reduces the total welding process cost per meter.
No post process
In traditional welding processes, almost always needs to spend long time for cleaning and preparing the welded surfaces. But with this newly developed technology, laser welding, in most cases no post process needs to be done.
The main differences between traditional and laser welding can be checked here too
Laser welding penetration
1000W | 1500W | 2000W | |||
Stainless steel | 2 mm | stainless steel | 3 mm | stainless steel | 4 mm |
Galvanized sheet | 2 mm | Galvanized sheet | 3 mm | Galvanized sheet | 4 mm |
Carbon steel | 2 mm | Carbon steel | 3 mm | Carbon steel | 4 mm |
Aluminum | 1.5 mm | Aluminum | 2.5 mm | Aluminum | 3.5 mm |
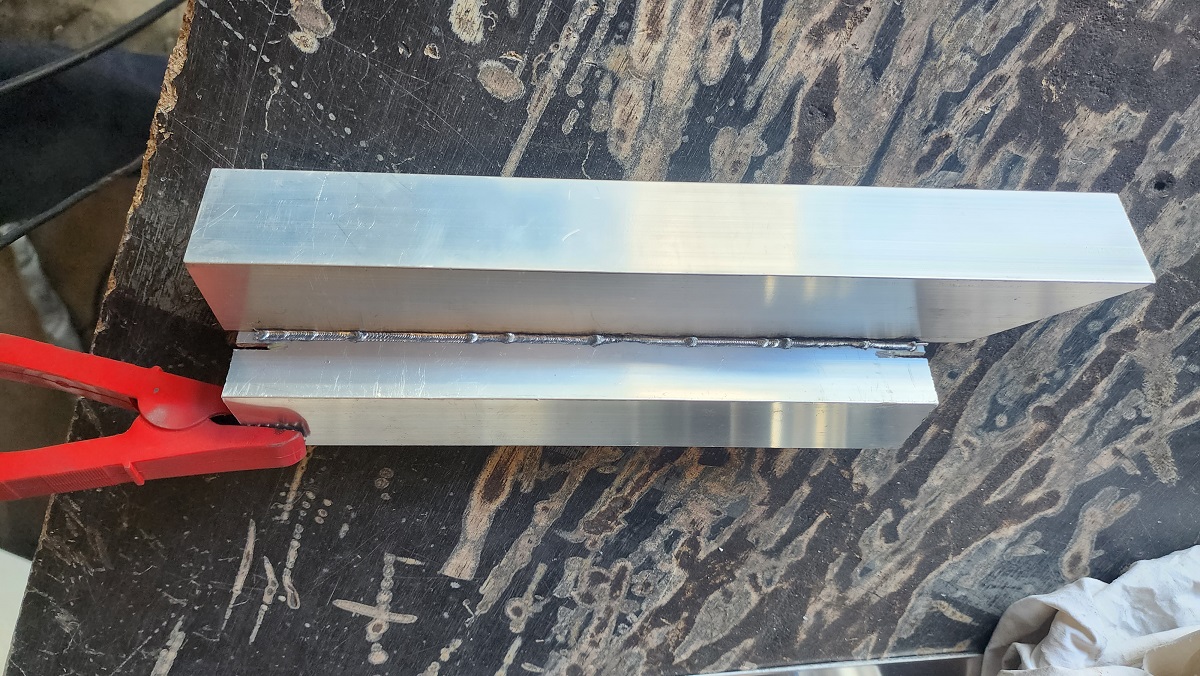
laser welding machine price
1000W | 1500W | 2000W |
A$14,500 | A$17,000 | A$22,000 |
Laser welder parameters
Welding Gun
- Smart internal design, good interactive control system, enlarged tolerance range of processing parts and weld width, and taking advantage of small laser spot and better weld formation.
- No Skilled Worker required!
While processing, wire filling welding or no wire filling is selectable, according to the product.
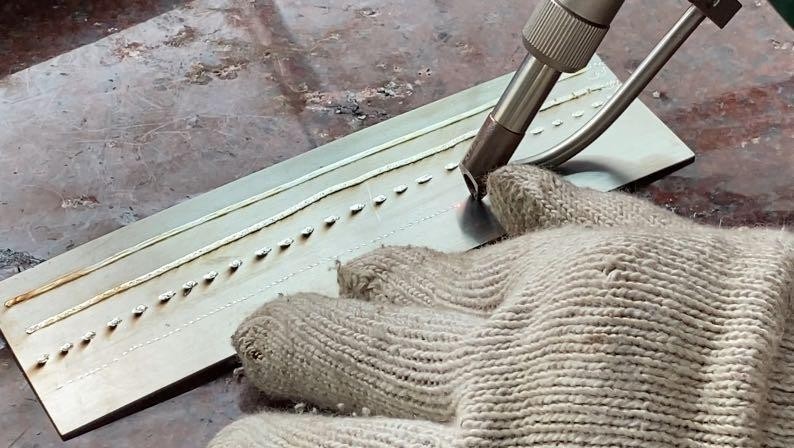
CW mode: continuous welding
PWM mode: wobble welding
Argon Arc mode: spot welding
QCW mode: Pulse welding
This laser welding machine system includes integrated touch screen control system, laser control system, galvanometer control system, and laser safety lock function. It has a variety of welding modes, the width of the spot can reach 0.2-5mm, which solves the uneven butt welding problems, and also the width of the beam is adjustable according to the actual product needs. This improves the fusion width and depth compared to traditional hand-held welding.
This laser welding system has adjustable beam and frequency setting (0-46HZ) to adjust the frequency according to the thickness of the plate, which solves the problem of over-burning caused by the high single-point power of traditional hand-held welding.
Different tips
There are 3 laser welding tips and one cutting tip, described below.
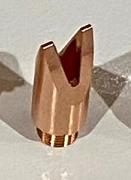
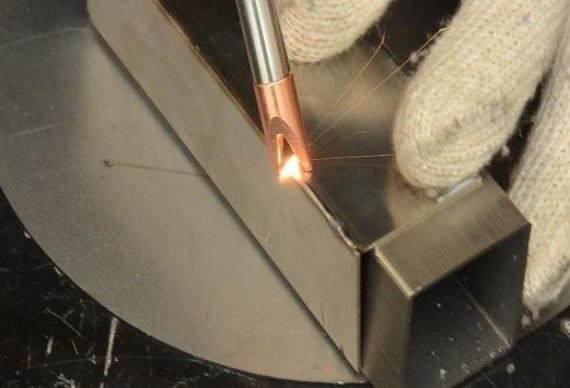
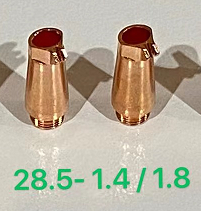
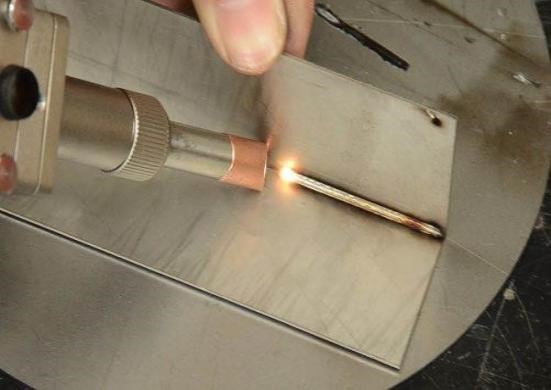
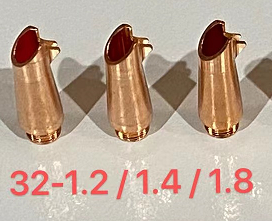
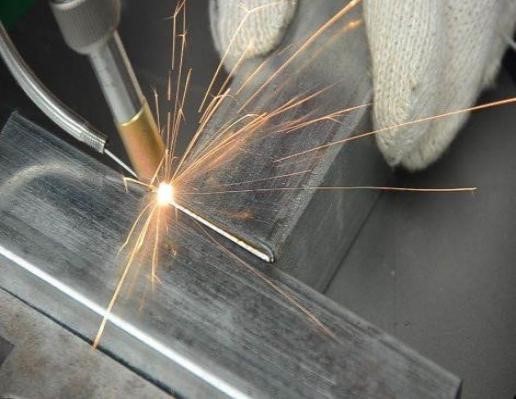

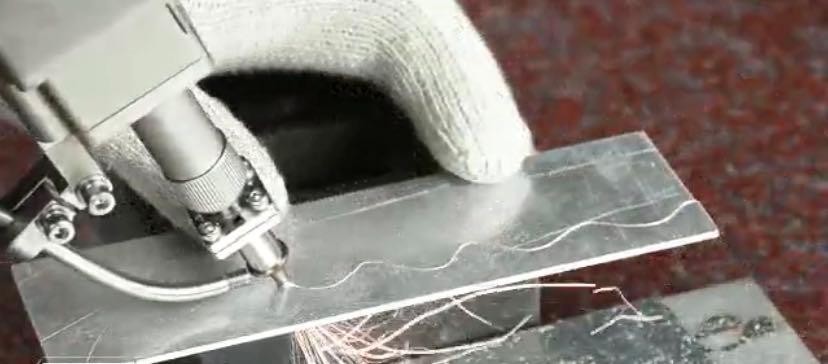
Raycus 1000W laser source details described here
Raycus laser source
For stock and availability, please send us an email to sales@pdmach.com.au
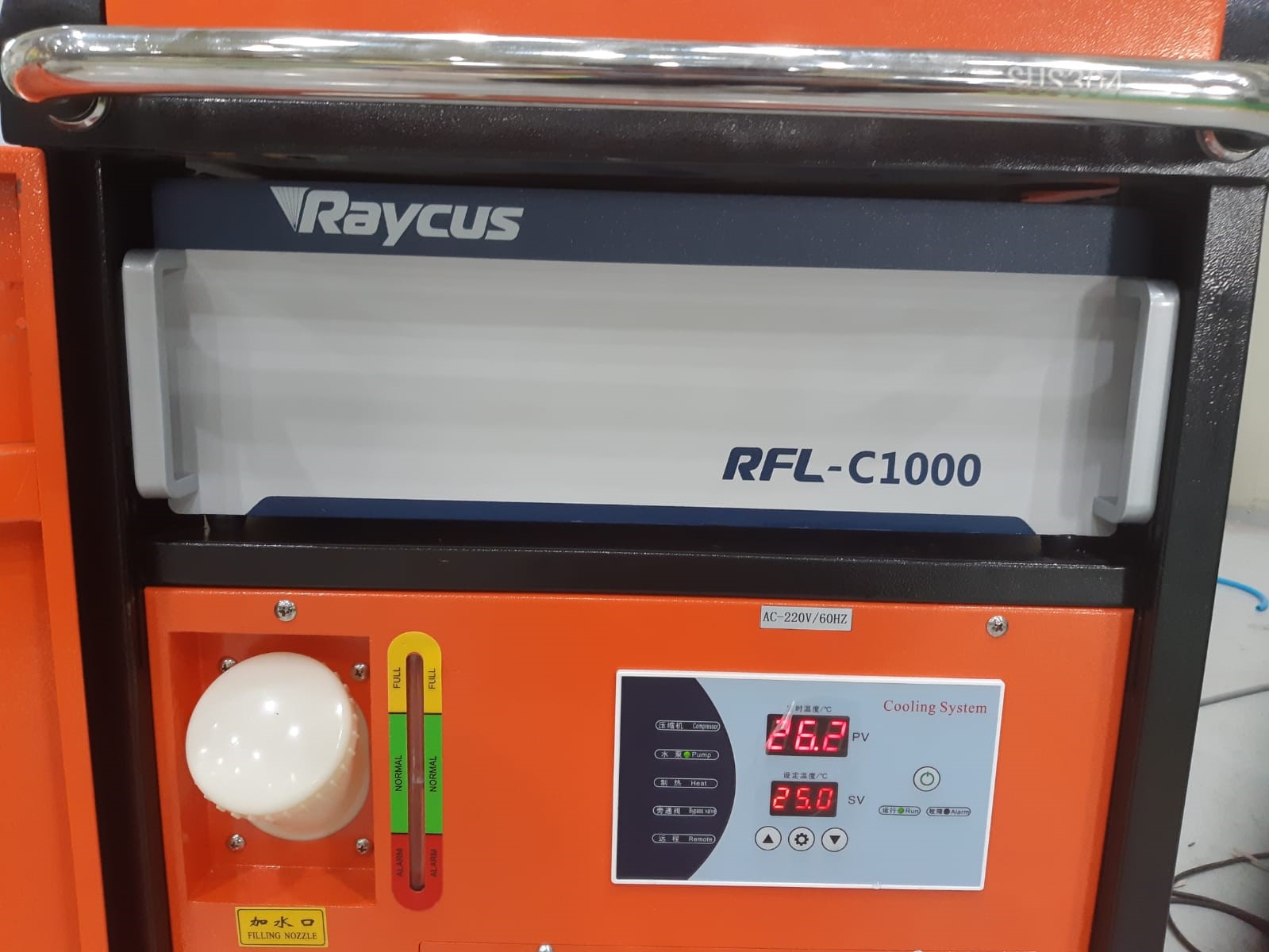
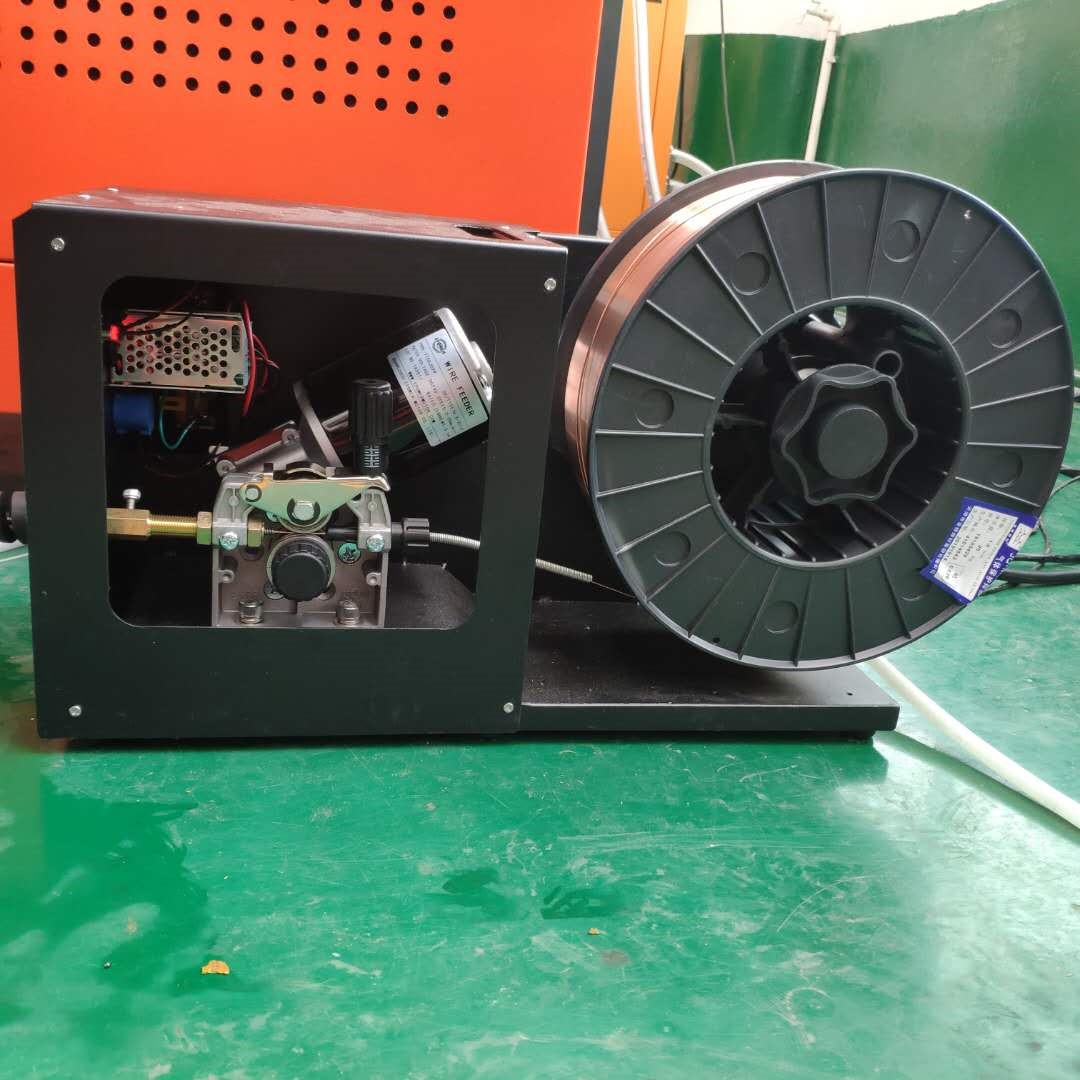
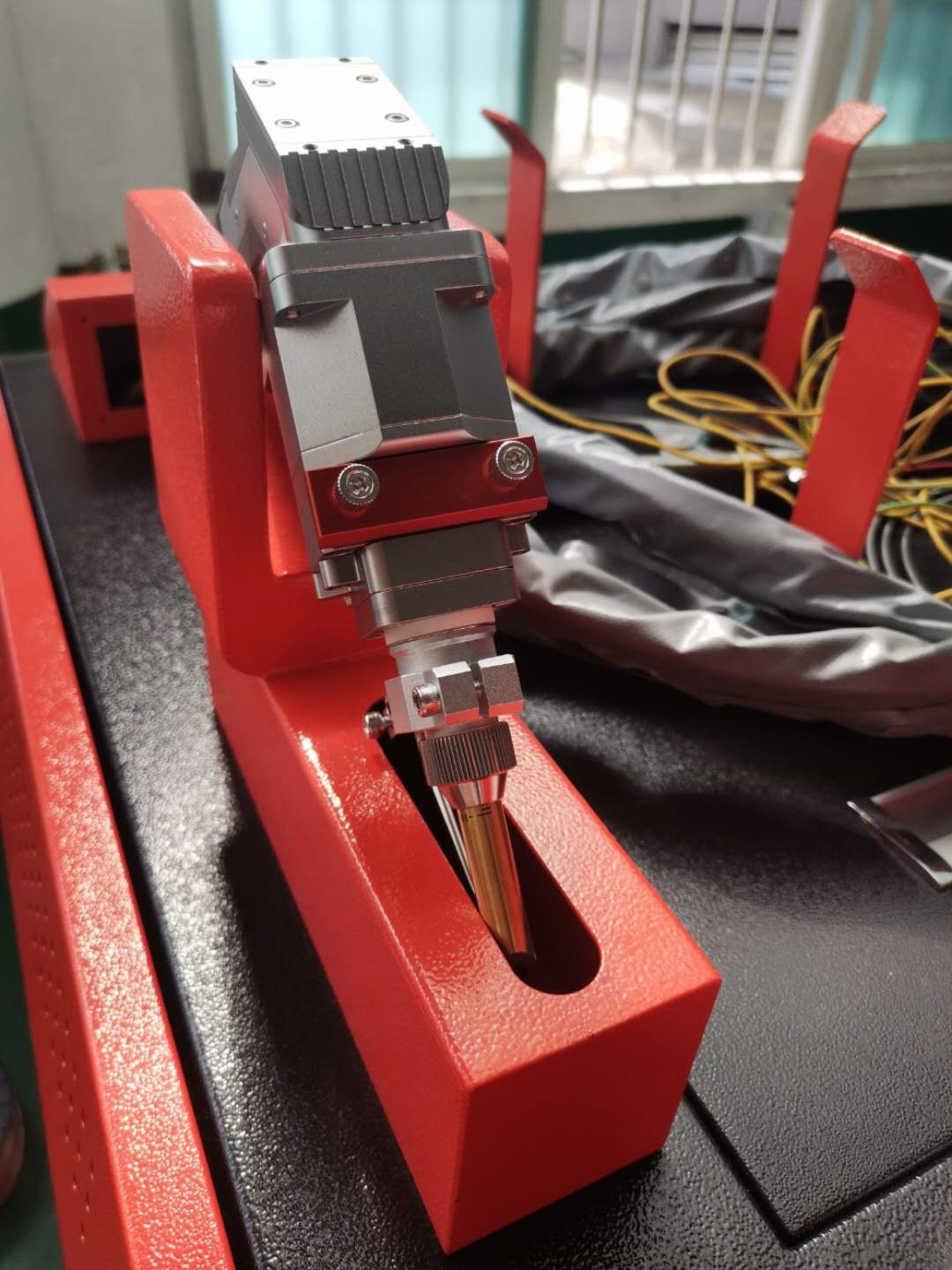
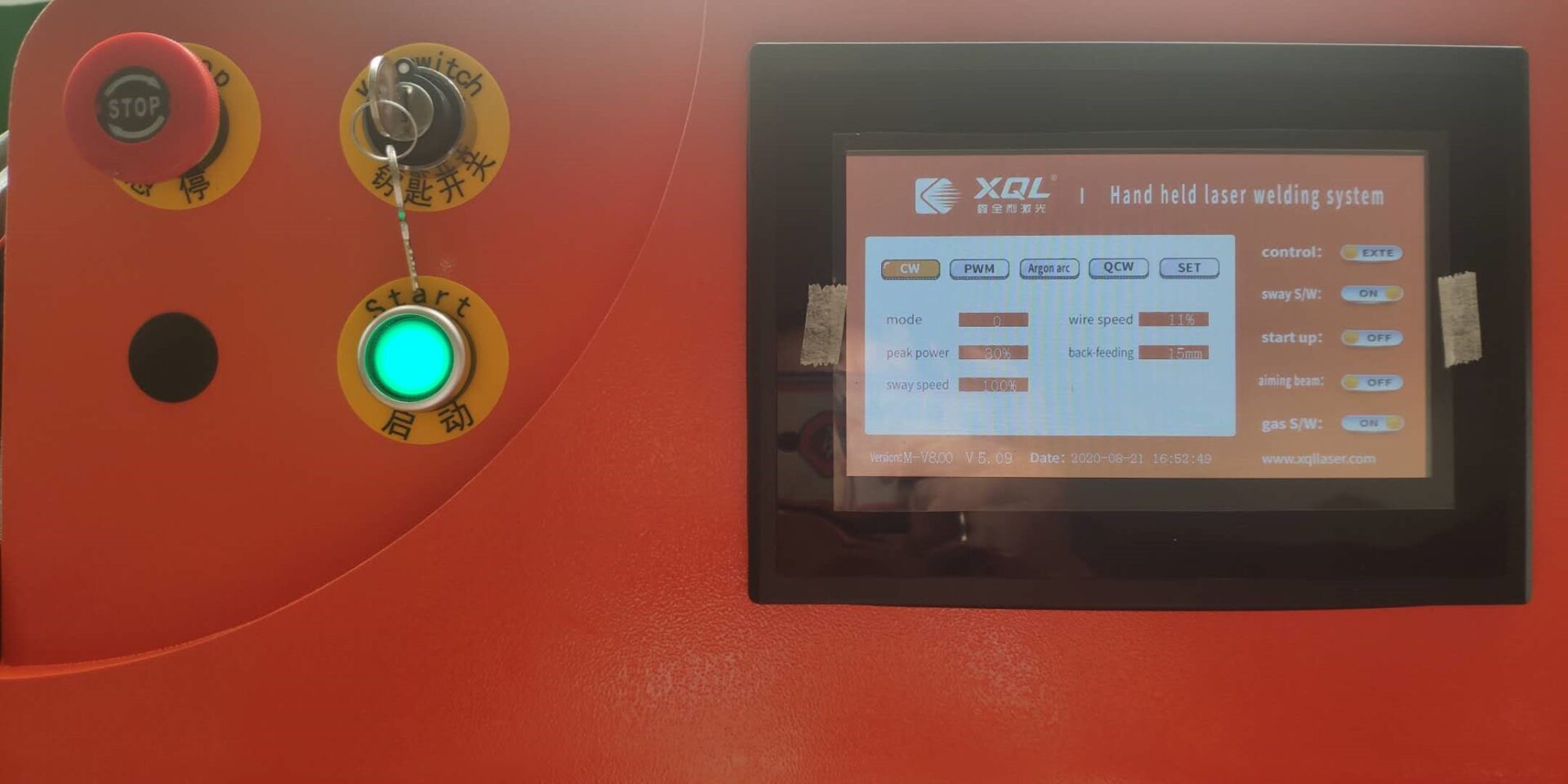
Laser Welding Samples
Very precise welding on stainless steel parts
Handheld Laser Welding Process Reference
- The thicker the plate, the thicker the welding wire, the greater the power and the slower the wire feeding speed.
- The lower the power is, the whiter the welding surface will be, and the higher the power will be, the welding seam will change from light to black, and one side will be formed at this time.
- The thickness of the welding wire should not be larger than the thickness of the plate, and the thickness of the welding wire should affect the fullness of the weld
- The thinner the wire, the lower the scanning width
Material | Thickness (mm) | Scanning speed (mm/s) | Scanning width mm | Power | Wire size | Joint | Status | Feed speed (cm/min) |
---|---|---|---|---|---|---|---|---|
Carbon steel | 0.5 | 400 | 2.5 | 220 | ER0.8 | T Joint | 100% | 100 |
Carbon steel | 0.5 | 400 | 2.5 | 220 | ER0.8 | in-Comer Joint | Yellowish | 100 |
Carbon steel | 0.5 | 400 | 2.5 | 220 | ERO.8 | out-Comer Joint | 100% | 100 |
Carbon steel | 1 | 400 | 2.5 | 330 | ER1.0 | T Joint | 90% | 80 |
Carbon steel | 1 | 400 | 2.5 | 380 | ER1.0 | in-Comer Joint | Yellowish | 80 |
Carbon steel | 1 | 400 | 2.5 | 380 | ER1.0 | out-Comer Joint | 70% | 90 |
Carbon steel | 2 | 400 | 3 | 700 | ER1.2 | T Joint | 100% | 70 |
Carbon steel | 2 | 400 | 3 | 700 | ER1.2 | in-Comer Joint | white | 70 |
Carbon steel | 2 | 400 | 3 | 700 | ER1.2 | out-Comer Joint | 100% | 60 |
Carbon steel | 3 | 400 | 3 | 1200 | ER1.2 | T Joint | 100% | 65 |
Carbon steel | 3 | 400 | 3 | 1200 | ER1.2 | in-Comer Joint | white | 75 |
Carbon steel | 3 | 400 | 3 | 1200 | ER1.2 | out-Comer Joint | 80% | 60 |
Carbon steel | 4 | 400 | 3.5 | 1500 | ER1.6 | T Joint | 100% | 60 |
Carbon steel | 4 | 400 | 3.5 | 1500 | ER1.6 | in-Comer Joint | 100% | 60 |
Carbon steel | 4 | 400 | 3.5 | 1500 | ER1.6 | out-Comer Joint | 80% | 60 |
Carbon steel | 5 | 400 | 3.5 | 1700 | ER1.6 | T Joint | 100% | 60 |
Carbon steel | 5 | 400 | 3.5 | 1700 | ER1.6 | in-Comer Joint | 100% | 60 |
Carbon steel | 5 | 400 | 3.5 | 1700 | ER1.6 | out-Comer Joint | 80% | 60 |
Carbon steel | 6 | 400 | 4 | 2000 | ER1.6 | T Joint | 80% | 60 |
Carbon steel | 6 | 400 | 4 | 2000 | ER1.6 | in-Comer Joint | 60% | 60 |
Carbon steel | 6 | 400 | 4 | 2000 | ER1.6 | out-Comer Joint | 60% | 60 |
Carbon steel | 6 | 400 | 3.5 | 2200 | ER1.6 | T Joint | 100% | 60 |
Carbon steel | 6 | 400 | 3.5 | 2500 | ER1.6 | in-Comer Joint | 100% | 60 |
Carbon steel | 7 | 400 | 3 | 2600 | ER1.6 | T Joint | 100% | 50 |
Carbon steel | 7 | 400 | 3 | 2800 | ER1.6 | in-Comer Joint | 100% | 50 |
Carbon steel | 8 | 400 | 3 | 3000 | ER1.6 | T Joint | 100% | 45 |
Carbon steel | 8 | 400 | 3 | 3000 | ER1.6 | In-Corner | 100% | 45 |
Material | Thickness (mm) | Scanning speed (mm/s) | Scanning width mm | Power | Wire size | Joint | Status |
---|---|---|---|---|---|---|---|
Stainless steel | 1 | 400 | 2.5 | 200 | ER304 1.0 | White | |
Stainless steel | 1 | 400 | 2.5 | 320 | ER304 1.0 | Color | |
Stainless steel | 1 | 400 | 2.5 | 350 | ER304 1.0 | Color | |
Stainless steel | 2 | 400 | 2.5 | 600 | ER304 1.0 | T Joint | 100% |
Stainless steel | 2 | 400 | 2.5 | 450 | ER304 1.0 | T Joint | Blue & White |
Stainless steel | 2 | 400 | 2.5 | 260 | ER304 1.0 | In-Corner Joint | Gold |
Stainless steel | 2 | 400 | 2.5 | 200 | ER304 1.0 | T Joint | Yellowish |
Stainless steel | 3 | 400 | 3 | 550 | ER304 1.2 | T Joint | Color |
Stainless steel | 3 | 400 | 3 | 700 | ER304 1.2 | In-Corner Joint | 70% |
Stainless steel | 3 | 400 | 3 | 800 | ER304 1.2 | T Joint | Single forming |
Stainless steel | 4 | 400 | 3 | 1000 | ER304 1.2 | T Joint | Color |
Stainless steel | 4 | 400 | 3 | 1200 | ER304 1.2 | In-Corner Joint | 70% |
Stainless steel | 4 | 400 | 3 | 1500 | ER304 1.2 | T Joint | Single forming |
Stainless steel | 5 | 400 | 3 | 1500 | ER304 1.6 | In-Corner Joint | Color |
Stainless steel | 5 | 400 | 3 | 1500 | ER304 1.6 | T Joint | 50% |
Stainless steel | 5 | 400 | 3 | 1700 | ER304 1.6 | Out-Corner Joint | 80% |
Stainless steel | 6 | 400 | 3 | 1500 | ER304 1.6 | T Joint | 50% |
Stainless steel | 6 | 400 | 4 | 1700 | ER304 1.6 | Out-Corner Joint | 100% |
Stainless steel | 6 | 400 | 5 | 1900 | ER304 1.6 | In-Corner Joint | 90% |
welding effect of 0.5mm stainless steel, inside corner
Parameter setting: 0.8 stainless steel wire, scanning speed 350, scanning width 2, peak power 350, duty
cycle 100, frequency 2000
As shown in Figure 10-1-1, the emitted light penetrates to the plate, and the amount of deformation is large, so we reduce the power to deal with it
Parameter setting: 0.8 stainless steel wire, scanning speed 350, scanning width 2, peak power 260, duty cycle 100, frequency 2000
The amount of deformation has been reduced, but it is still easy to burn through when the light is first emitted, so we continue to reduce the power. As shown in Figure 10-1-2.
Parameter setting: 0.8 stainless steel wire, scanning speed 350, scanning width 2, peak power 200, duty cycle 100, frequency 2000
The effect is shown in Figure 10-1-3, and when the width is increased to 3, it is shown in Figure 10-1-4.
The above parameters debugging process, are for reference only, and the actual conditions shall prevail.
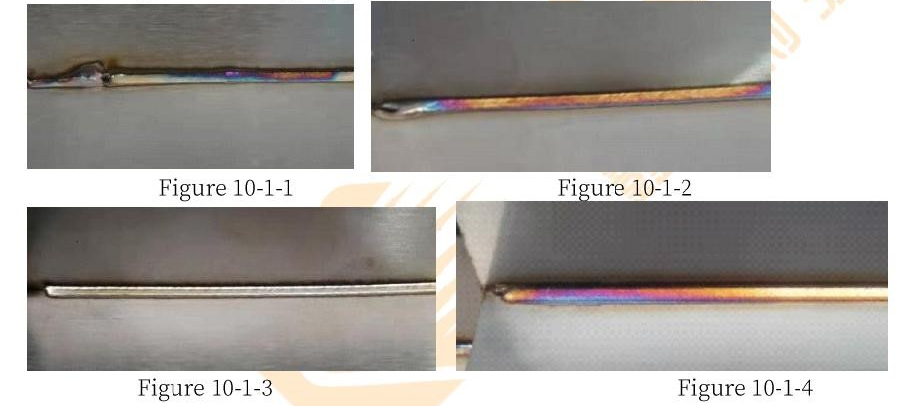
For aluminum welding refer to the stainless steel process, and the power can be increased by 20%-30%. In addition, there are differences in focus, which need to be adjusted manually.
Wire feeder
Features
touch screen display, four-wheel dual-drive wire feeding mechanism, wire feeding speed 25-600cm/min (adjustable), support continuous wire feeding mode and pulse wire feeding mode
Wire details
0.8/1.0/1.2/1.6mm, 2.0/2.5mm can be customized
- Stainless steel welding wire is used for stainless steel materials
- Iron wire is used for carbon steel/galvanized sheet material
- Aluminum wire is used for aluminum material (we recommend using alloy aluminum above series 5 for aluminum welding wire, which has high hardness and is not easy to get stuck)
Welding Wire/Feed Roller Installation
CAUTION: DO NOT USE FLUX-CORED WELDING WIRE.
- Adjust the strength of the roller through the inner hexagon, to keep it not too tight or too loose, and there is no jamming during wire feeding (Factory preset, no need to adjust in normal situation)
- Cover the CAP after adjustment (Figure 11-1-2)

- There are two wire feed rollers working in one pair. The roller has two sizes of notch, corresponding to different welding wire diameters.
- Be sure to install it accordingly. If 1.2 welding wire is installed, the side with the 1.2 MARK on the wire feed roller is facing the outside of the machine.
- Be sure welding wire stick in the notch before fixing the clamp (Figurel1-1-3)
Installation of Wire Feeding Tube
Before installing the wire feed tube to the machine, first remove the copper nozzle at the other end of the tube. Install the corresponding size of copper nozzle only after finish installed the wire feeding tube metal part. (Figure 11-1-4)

Insert wire into the wire feeding tube, to a suitable position, and fasten the lock screw. (Figure 11-1-5)
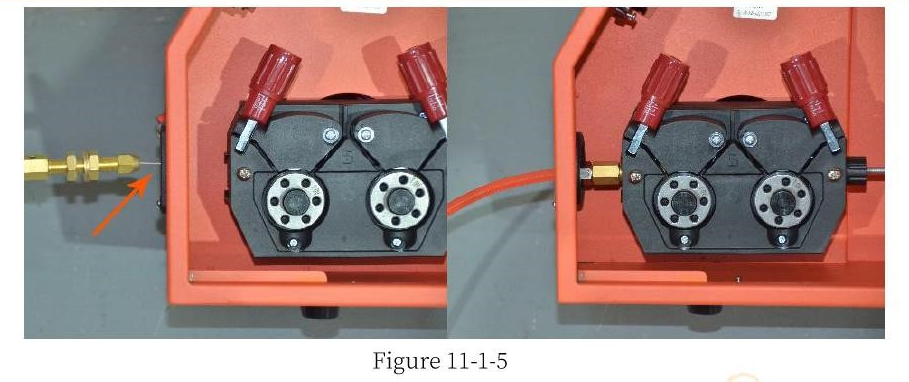
Caution not to touch the wheel. (Figure 11-1-6)

Check to make sure you use the right size of welding nozzle to fit the welding wire. (Figure 11-1-7)
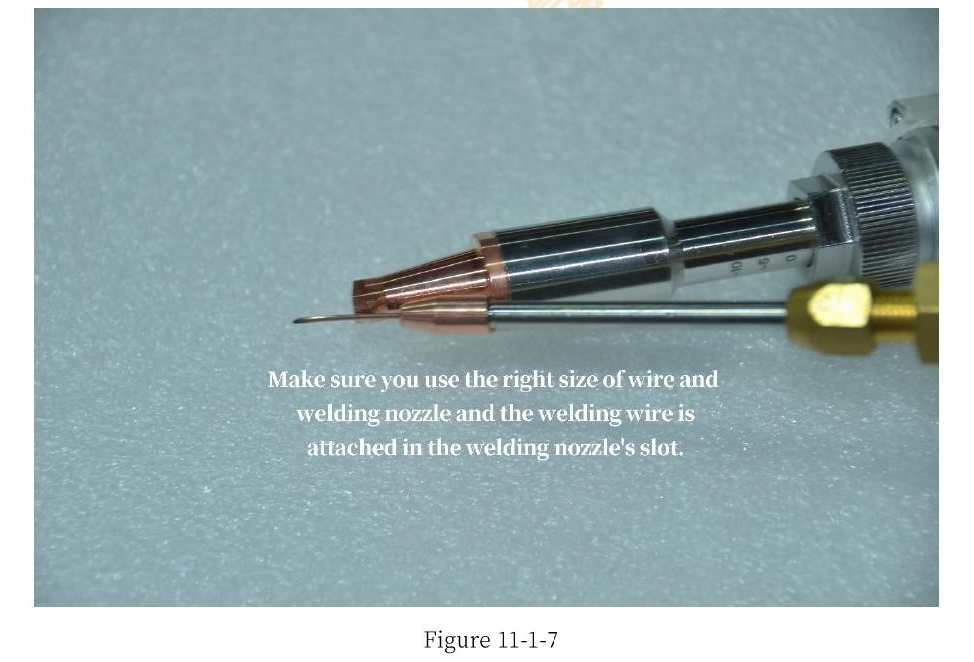
Sample Videos
Precision welding on stainless steel
Because of the total technology revolution in laser welding, achieving perfect welding result is easy!
Welding tips
Different tips used for different welding position and configurations
Stainless steel sign and letters
Laser welding widely used in signage for making illuminated letters
Handheld laser welder
There are two versions for laser welder, handheld and table welder with CCT camera
Welding in different angles
Easy welding
Aluminum welding
Unskilled welding with laser
Mass production with laser technology
About the manufacturer
Guangdong Xinquanli Laser CNC Equipment Co., Ltd. is a high-tech enterprise integrating R&D, design, production, sales and service. It is located in Shunde National Economic and Technological Development Zone, Foshan City, Guangdong Province. The main products are laser cutting machines, laser welding machines, and robot automation solutions.
Relying on the accumulation of 15+ years of focusing on industry development, Xinquanli Laser has won numerous reputations but always insists on innovation and leadership.
In promoting the standardization of the industry, Xinquanli has successively participated in the compilation of “the team standard drafting of the “Handheld Laser Welding Machine” and the “National Standard for Testing Method of Energy consumption in Welding Processing” and other work.